印刷技術の継続的な発展に伴い、多くの有名な印刷ブランドの機器の性能はますます向上しているだけでなく、自動化の程度も継続的に向上しています。インク カラー リモート コントロール システムは、多くのインテリジェント印刷の「標準構成」となっており、印刷製品のインク カラーの制御が便利で信頼できるものになっています。しかし、実際の印刷工程では、印刷物のロットごとに安定したインク色を実現することは容易ではありません。インクの色の大きな違いによって引き起こされる品質上の問題は、生産中にしばしば発生し、会社に損失をもたらします。
印刷前に経験に基づいた事前調整をしっかり行う必要があります
まず、プルーフの範囲に応じて、各色グループのインキつぼのインキ量を大まかに調整します。印刷皿。この作業は、インク リモート コントロール システムを備えたマシンで簡単に完了できます。これは 80% 以上と推定されるはずです。大きな色の違いを避けるため、印刷中にインク量を大きな範囲で調整しないでください。
第二に、生産プロセスシートの要件と製品の特性に従って、正式な印刷中に急いでしまうことを避けるために、フィーダー、用紙コレクション、インク性能、圧力サイズなどのリンクを事前に調整します。その中でも、フィーダーが確実に、連続して、安定して用紙を給紙できることが最も重要です。経験豊富なオペレーターが、まず紙のフォーマットや厚さに応じて、吹き込み、吸引、押え、押えバネ、紙押さえホイール、サイドゲージ、フロントゲージなどを事前調整し、各コンポーネント間の動きの調整関係を整えます。フィーダーが用紙をスムーズに送り、フィーダーの衝突によるインクの色合いの違いを回避します。経験豊富な作業者がフィーダーを事前に調整することをお勧めします。
また、印刷適性を高め、正常に印刷できるよう、使用する紙の質や印刷物の画像・文字領域のサイズに応じて、インクの粘度、流動性、乾燥性を事前に適切に調整する必要があります。 。ゴム布や印刷版上の紙毛やインク肌を清掃するために頻繁に停止することにより、インクの色が不均一になってはいけません。印刷途中で各種接着剤除去剤やインキ油を添加すると、確実に色ずれが発生します。
つまり、機械を起動する前に事前調整をしっかり行うことで、正式な印刷後の失敗を大幅に減らすことができ、機長はインクの色に集中する時間とエネルギーを得ることができます。
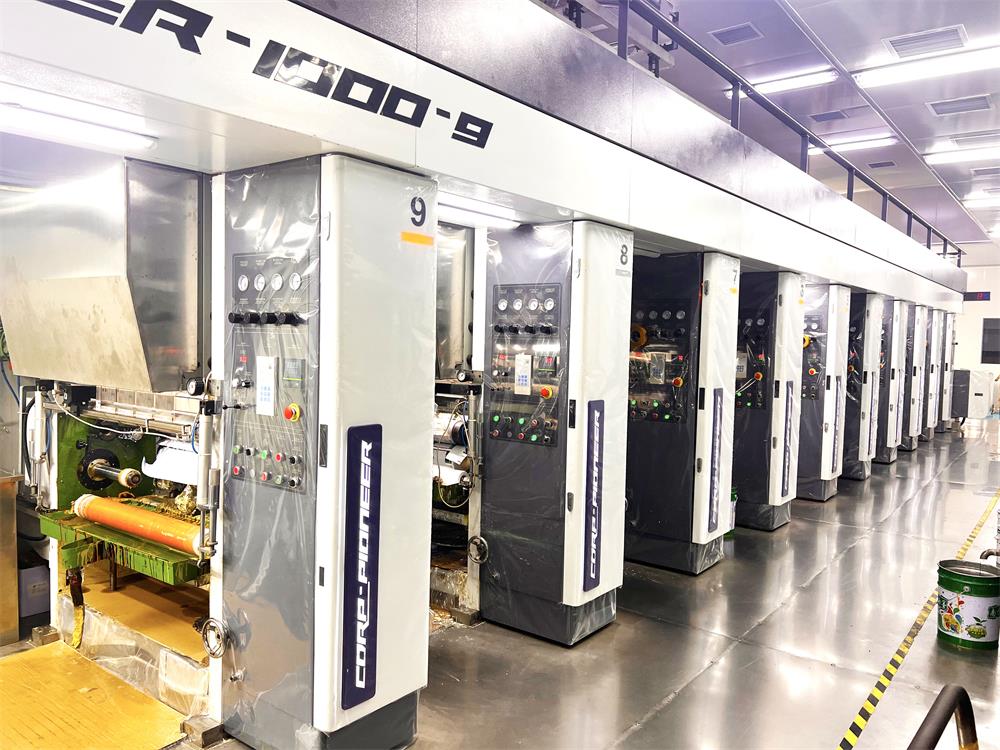
水とインキローラーの圧力を正しく調整する
印刷プロセス中、一貫したインク色の印刷物を得るには、印刷版の画像とテキスト部分に適切な量のインクを連続的かつ均一に塗布する必要があります。したがって、良好なインク転写を実現するには、インキ ローラーとインキ ローラー、およびインキ ローラーと印刷版が適切な接触と回転関係を維持する必要があります。この作業を丁寧に行わないと、インクの色が均一になりません。したがって、水ローラーとインキローラーを取り付けるたびに、隙間ゲージを使用して張力をテストする従来の方法ではなく、インキバーを転がしてそれらの間の圧力を1つずつ調整する方法が使用されます。さまざまな人的要因による実際の誤差が大きく、多色機や高速機では禁止すべきである。ローリングインキバーの幅は、通常4~5mmが適当である。最初にインキ転写ローラーとインキ糸引きローラーの間の圧力を調整し、次にインキローラーとインキ糸引きローラーと印刷版胴の間の圧力を調整し、最後に水転写ローラーと版水ローラーの間の圧力を調整します。水引きローラー、中間ローラー、版水ローラーと印刷版胴間の圧力。これらの水路間のインクバーは 6 mm である必要があります。
特にトランスミッションでの高速摩擦が続くとインクローラーの直径が小さくなるため、2 ~ 3 か月使用した後に装置を再調整する必要があります。インキローラーにインクが溜まると、インキローラー間の圧力が小さくなり、インキを転写できなくなります。印刷を継続するためにフィーダーが一時停止または停止すると、このときのインクの量が多くなり、最初の数十枚、場合によっては数百枚のインクの色が濃くなり、理想的な水性インクとインクのバランスを達成することが困難になります。この欠陥は通常、見つけるのが簡単ではありませんが、より細かい印刷物を印刷する場合にのみ顕著になります。つまり、この点での作業は細心の注意を払い、その方法は科学的でなければなりません。そうでないと、水、インクバー、版画の口と尾のインクの深さが異なり、人為的に欠陥が発生し、印刷の難易度が高くなります。手術。
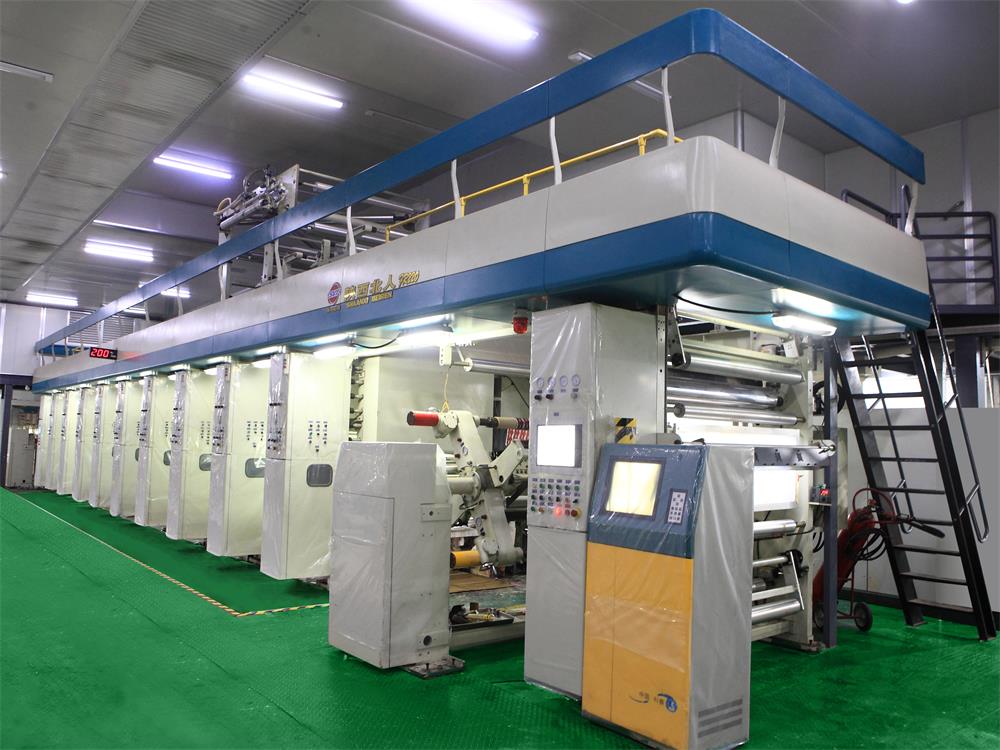
水性インクとインクのバランスを実現する
誰もが知っているように、水とインクのバランスはオフセット印刷の重要な部分です。水が多くインクの量が多い場合、インクは油中水型に乳化し、印刷物の品質は確実に理想的ではなくなります。著者は長期にわたる実践を通じて、いくつかのテクニックを探求してきました。
まず、水とインク ローラーの間の圧力関係が適切に調整されていること、湿し水とイソプロピル アルコールの含有量が一般的な基準を満たしていることを確認します。これに基づいて、機械の電源を入れ、水ローラーとインキローラーを閉じてから、機械を停止して印刷版を確認します。版端のベタつき汚れが3mm程度あるくらいがベストです。このときの水量を印刷の初期水量とすれば、一般的なグラフィック製品の正常な印刷が保証され、基本的に水とインクのバランスが得られます。
第二に、印刷版の面積が大きい、紙の表面が粗い、インクに添加剤を加える必要性、印刷速度、印刷速度の変化などの他の要因に応じて、水の量を柔軟に調整できます。気温と湿度。
また、印刷を開始したばかりのときは本体温度が低く、1 ~ 2 時間高速で動作させると本体温度、特にゴムローラーの温度が上昇することもわかりました。 2倍以上、あるいはそれ以上に上昇します。このとき、水性インクが新しいバランスに達するまで、水の量を徐々に増やす必要があります。
水とインクのバランスを達成するのは簡単ではないことがわかり、オペレーターはそれを弁証法的に秤量して使用する必要があります。インクの色の安定性をコントロールすることが難しく、高品位な印刷物を印刷することができません。
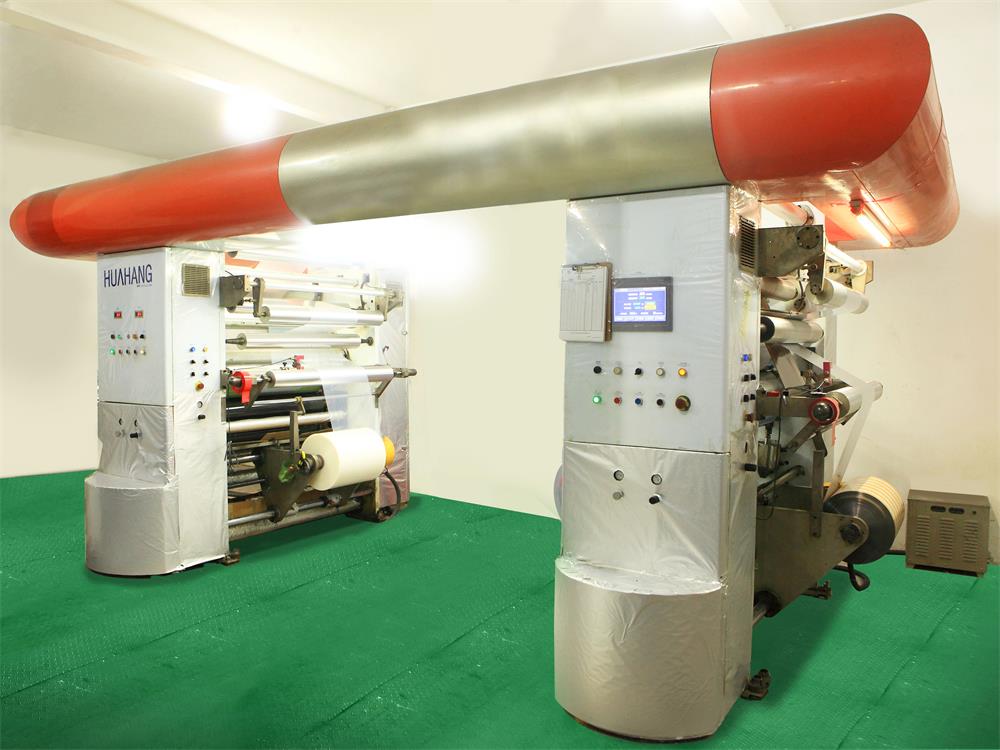
校正と色順の調整
生産現場では、お客様から提供されたサンプルが非常に標準的ではない、または校正なしでカラー インクジェット ドラフトのみが提供されるなど、このような状況に遭遇することがよくあります。このとき、具体的な状況を分析する必要があり、厳密にインク量を増やしたり減らしたりして校正の効果を追う方法は使えません。たとえ最初は校正刷りに近かったとしても、インクの色の安定性は保証できず、最終的な印刷物の品質は保証できません。この点、印刷工場は真剣かつ責任ある態度で顧客と積極的にコミュニケーションを図り、サンプルの問題点や修正案を指摘し、同意を得た上で印刷前に適切な調整を行う必要があります。
製造現場では、多色機の印刷色の順序は通常、インクの粘度によって決まります。多色印刷ではインクをウェット・オン・ウェットで重ね合わせるため、最適な重ね合わせ率を得ることで初めて安定した均一なインク色を印刷することができます。印刷の色順序の配置は、印刷製品の特性と品質要件に準拠する必要があり、変更しないでください。同時にインクの粘度も調整できます。たとえば、紫色のカバーとスカイブルーのカバーでは印刷の色の順序が異なります。前者では最初にシアン、2 番目にマゼンタ、後者では最初にマゼンタ、2 番目にシアンです。そうしないと、オーバープリントされたカラーが斑点になり、滑らかでも安定でもありません。たとえば、主に黒を含むプリントの場合、黒はできるだけ最後の色グループに配置する必要があります。こうすることで黒の光沢が良くなり、機械内部の傷や色の混入を防ぎます。
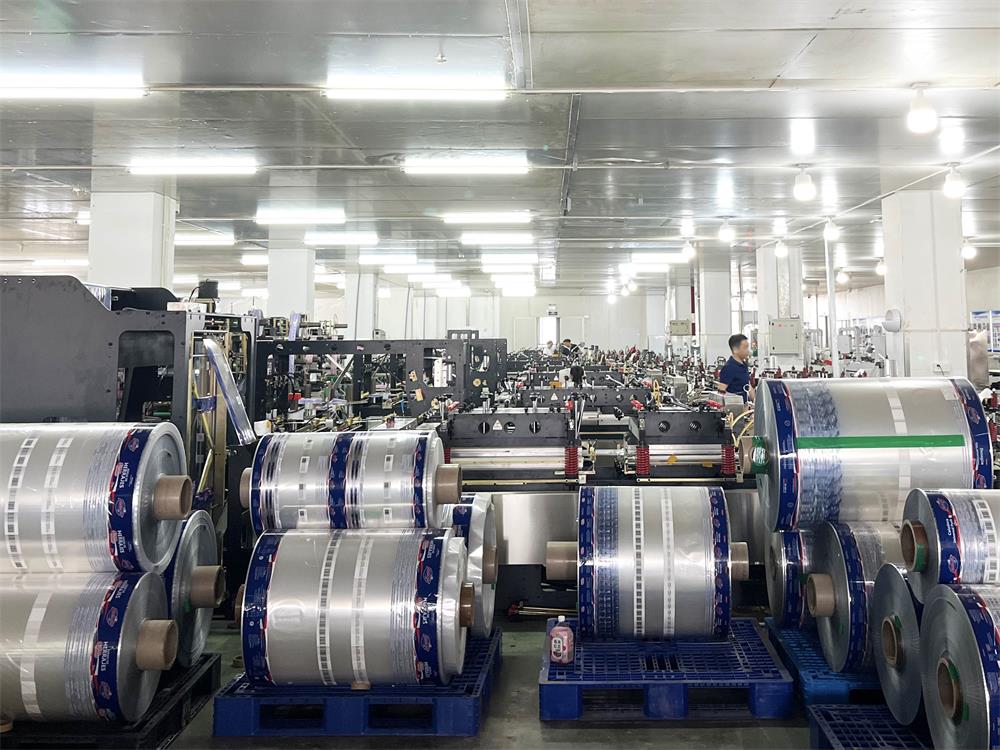
良い運転習慣を身に付け、仕事に対する責任を強化する
いかなる仕事においても、高い責任感と高い品質意識を持たなければなりません。私たちはプロセスの運用を標準化し、「3 つのレベル」や「3 つの勤勉」などの伝統的な良い習慣を遵守する必要があります。サンプルの頻繁な比較を例に挙げます。サインサンプルをサンプル上で比較すると、距離、角度、光源などの違いにより、視覚的に偏り、インクの色が不均一になります。この時点で、署名サンプルをサンプルから取り出して慎重に比較する必要があります。長期間使用する印刷版は、版交換によるインクの色のずれを軽減するためにベーキングする必要があります。ゴム布は頻繁に掃除する必要があり、インクの色を安定させるために、掃除のたびにさらに多くの吸い取り紙を置く必要があります。フィーダーが一時停止された後、印刷されたばかりの 5 ~ 6 枚のシートは濃すぎるため、引き抜く必要があります。印刷速度は速すぎてもいけません。重要なことは、マシンを安定して正常に保つことです。インキ壷にインキを加える際、新しいインキは硬く流動性が悪いため、インキ量に影響を与えたり、インキの色ずれが生じたりしないように、数回かき混ぜる必要があります。
オペレーターは引き続き注意深く学習、観察、分析し、あらゆる面からインクの色の変化に影響を与える要因を見つけ出し、それらを適切に防止および克服するための対応措置を講じ、インクの色の安定性と一貫性を向上させるよう努める必要があります。印刷物の品質を効果的に向上させます。
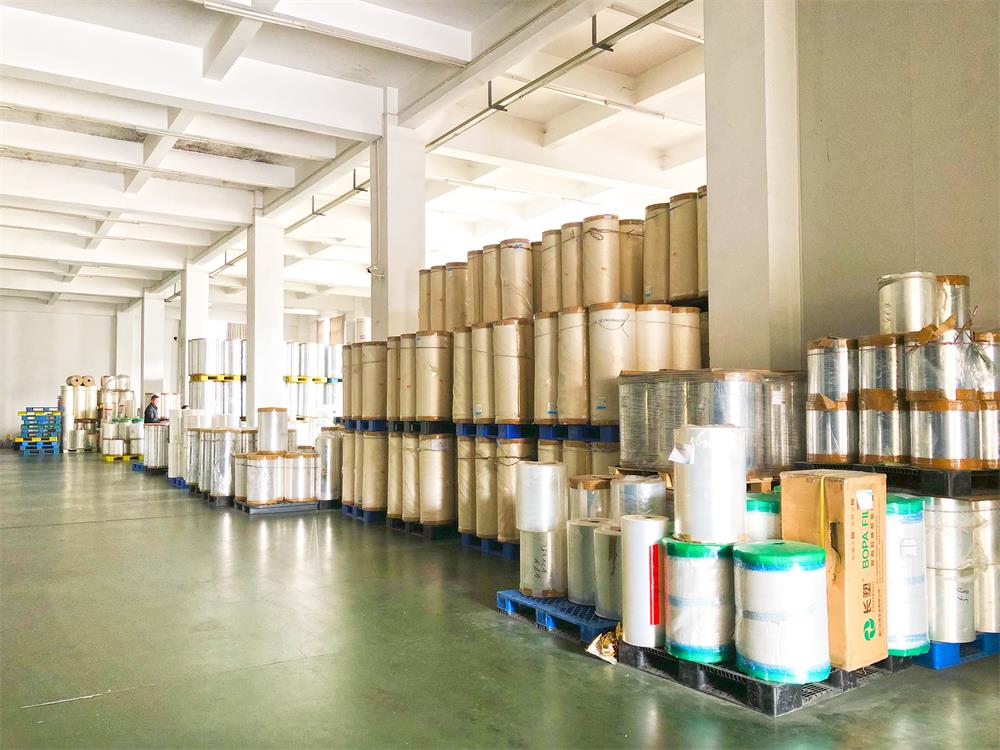
投稿日時: 2024 年 5 月 27 日